MV Switchgear, which executed two large contracts over the past two years involving manufacture, supply and installation of numerous air-insulated switchgear (AIS) panels for 11kV substations at the extensive new Kamoa-Kakula copper mine in the Democratic Republic of Congo (DRC), has subsequently been awarded a further contract for GELPAG solid insulated switchgear (SIS) units for more underground substations at the mine.
A total 233 of MV Switchgear’s well-known and widely-used SBV4E brand of AIS switchgear panels were produced and supplied by the division to equip surface and underground substations at the new mine. They comprised 140 panels for eight surface substations and 93 panels for five underground substations.
The latest contract for 149 GELPAG SIS units for eight underground substations, awarded late last year for delivery in August this year, came about as a result of having to address changes in underground conditions at the mine as mining operations progressed.
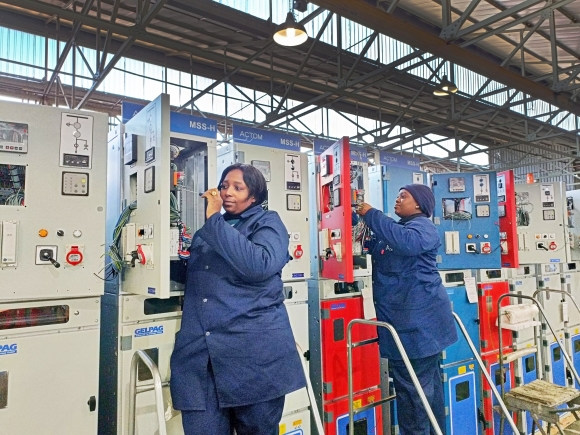
“Harsh environmental conditions such as high levels of humidity and dust were found to be present in these underground sections, necessitating having to introduce more specialised switchgear equipped to cope with these conditions,” said Rhett Kelly, MV Switchgear’s Design & Development Manager.
“In such a situation the choice is typically between fixed pattern gas-insulated switchgear (GIS) and solid-dielectric-insulated switchgear (SIS). We were confident in recommending to DRA Global of South Africa, the engineering consultants for the Kamoa project, our GELPAG SIS product for this purpose.”
With MV Switchgear experiencing growing demand for GELPAG since introducing it into the local market in late-2020, it recently arranged in collaboration with its overseas-based OEM partner to commence local manufacture of some of the product’s ancillary components.
“By taking this step we’ve substantially shortened the production lead times, as we can now manufacture the agreed locally produced components in parallel with the OEM’s production of the main product, thereby speeding up both final assembly of the product in our plant as well as delivery to the end-user,” Rhett said.
The Kamoa mine will be the first recipient of GELPAG panels in terms of the new arrangement.
Johan Jordaan, the division’s Technology Development Specialist, said: “The components being manufactured locally now and in the future are the LV compartment, internal arc ducting and the drop-down boxes for the cable terminations.
“While not normally required for the GELPAG product range, custom drop-down boxes have been designed to accommodate the 3-core cable terminations with core balance CT’s specified by the customer.
“To further speed up and simplify production and delivery, we’ve developed an LV connector system which allows the panel’s circuit-breaker, disconnector and earth switch wiring to interface with the LV control wiring via a standard multi-pin plug-and-socket system,” he added.
MV Switchgear has also developed a wiring test rig to enable it to test and verify the wiring of each LV compartment before the GELPAG panels they are to be connected to arrive from abroad.