Marthinusen & Coutts (M&C) and ACTOM Turbo Machines jointly successfully performed the General Overhaul (GO) of Sasol’s Secunda gas turbine driven 147MVA (120MW) generator.
Sasol uses a feed stream of natural gas piped from Mozambique to drive the 2 X 147MVA turbines and generators.
This major GO was performed after approximately 100 000 hours runtime.
Mike Chamberlain, M&C’s Marketing & Commercial Executive, who project managed the GO, said that in addition to the ACTOM bid being competitively priced, he believes that the good track records both M&C and ACTOM Turbo have independently established with Sasol on a variety of projects played an important part in its decision to award the GO contract to them.
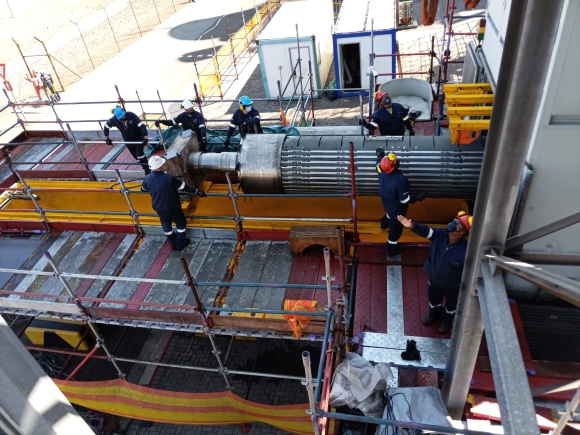
“In addition, M&C and ACTOM Turbo have successfully worked together on a substantial number of projects in the past,” Mike commented.
M&C was appointed lead contractor on the GO for the 147MVA generator and took direct responsibility for all the electrical work involved, while ACTOM Turbo was charged with the responsibility of executing all the mechanical work.
The core portion of the contract was carried out during a 34-day shutdown period late last year, when the generator’s 34t, 9m long, 1m diameter rotor was removed and transported to M&C’s Benoni Power Generation workshop for removal of the rotor’s coil retaining rings, inspecting and cleaning the windings and overhangs, plus high-speed balancing of the rotor, before being returned to site for reinstallation.
“At the same time testing and cleaning of the stator windings were carried out on site, and loose wedges were repaired. We also did in-situ Partial Discharge and Tan Delta testing, as well as end-winding resonance frequency tests on the 11kV stator,” said Mike.
The GO procedures were completed with the reassembly of the generator on site and performance of a test run witnessed by the client.
However, before any of the abovementioned GO procedures could be carried out, the teams were confronted during the 28-day lead-in period prior to the shutdown with unexpected complications they had to solve first.
Special equipment was provided for removal of the rotor out of the stator core, on a sliding rig with trolleys running on a track to bring it out into a central position on the frame structure, from where it could be lifted by a 120t mobile crane for transport to the workshop.
The rotor threading frame structure, comprising three steel A-frame pedestals anchored on concrete plinths, was intended to provide support to the rotor threading structure used to remove – and later re-install – the rotor.
“As a precaution before commencing the work, we assembled and checked the threading frame structure in our workshop. All the welds on the A-frame pedestals failed inspection and were re-welded,” said Mike.
“However, on site we found that the structure did not fit, due to cable racks and electrical boxes being in the way, so the railway beam was cut away to clear these obstructions. We also had to weld on extensions to the railway tracks to make it the right length.
“Furthermore, the railway track was inadequate for supporting the weight of the rotor, resulting in us having to increase its strength. It was also necessary to manufacture a new more stable coupling side trolley and modify the skid plate on which the sliding skid runs to ensure proper protection of the stator windings during removal of the rotor.”
The contract was completed within the shutdown period with days to spare.
”In executing this large and complex contract, M&C and ACTOM Turbo demonstrated their ability to perform a full electro-mechanical service, giving the customer one point of contact for the entire project,” Mike concluded.